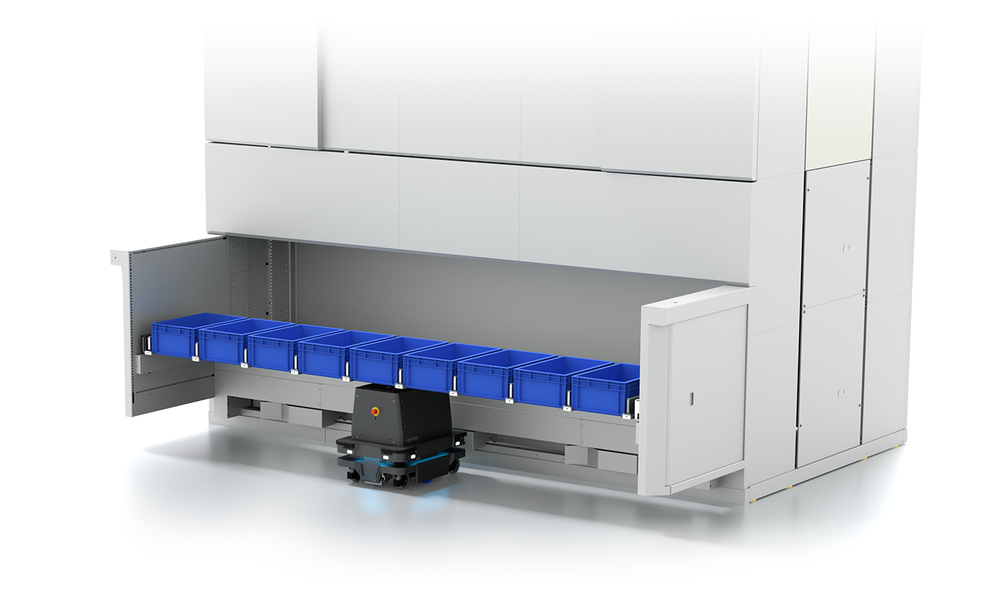
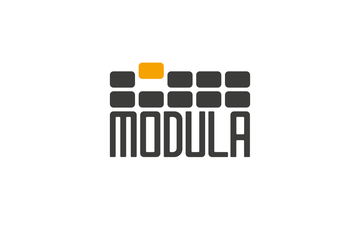
Disclaimer:
Mobile Industrial Robots are not responsible for the products displayed on the MiRGo platform. We only provide the information provided by the dealer partners, and the dealer partners are fully responsible for the product and the stated specifications.
Product Information
The vertical storage system is an automatic storage system that takes full advantage of the building’s height and thus has a very limited footprint.
The structure, the so-called VLM (Vertical Lift Module), has the shape of a tower and is made up of three columns: one at the front, one on the back and one in the middle. The column in the middle is the one in which the elevator moves, picking and repositioning the trays, while those on the front and back are used to store the trays themselves. The system is based on the “goods to person” method and in fact delivers the goods directly to the operator, improving picking operations and reducing the work and time required for order fulfillment.
Robots are able to transport materials picked from Modula automatic storage systems or from other storage systems. Picking operations can be done manually or automatically.
The combination of AMRs with the Modula vertical warehouses allows you to carry out the picking, storage and handling of goods in complete autonomy and allows operators to be able to devote themselves to higher value activities, far from dangerous or unhealthy areas.
The Modula WMS warehouse management software and that of the AMR robot are interactive with each other, thus ensuring precise synchronization of operations. This solution is both scalable and modular, as it is able to adapt to numerous environments with different characteristics, thanks to the speed of installation.
- Manual picking
- Automatic picking
- Pallet transport
- Hook and picking cart
- AMRs and anthropomorphic Cobots
MiR AMRの導入には、レールの設置や、既存の作業場の環境を変更する必要がありません。
Technical Information
Compatible with: MiR100, MiR250, MiR600, MiR1350
Unit height: from 3,300 mm to 16,100 mm
Unit height increment: 200 mm
Tray storage pitch: 25 mm
Tray width: from 1,500 mm to 4,100 mm
Tray depth: 654 mm - 857 mm - 1,257 mm
Net tray payload: 250 - 500 - 750 - 990 kg
Total net payload: from 40,000 kg to 80,000 kg (depending on model and configuration)
Total gross unit payload: up to 90,000 kg (depending on model and configuration)
Throughput: up to 120 trays per hour(depending on the configuration)
Operator interface: industrial console with 10.4” touchscreen technology
Number of bays: up to 3, also above ground level and on the same side
Types of bay: internal or external with single or dual delivery level
Maximum stackable height: 695 mm (bay S) / 895 mm (bay M) / 1,295 mm (bay XL)
Minimal energy consumption
Automatic weight check on tray return
Dynamic tray height storage
Load-bearing structure in galvanised steel
Eagle steel-reinforced toothed-belt transmission
Elevator guide system with 6 HDPE rollers per side
Company Description
Founded in 1987, Modula introduced its first VLM to the market. Since then it has developed a series of solutions for automated storage, ideal for any type of industrial environment and designed for a wide variety of product types: from small electronic or pharmaceutical components, to heavy and bulky objects such as molds or car parts and motors.
The success of Modula products has guaranteed the company a strong international expansion and allowed significant investments in highly automated production lines: all this to guarantee its customers increasingly technologically advanced and reliable solutions.
Modula now has 800 employees spread between its production plants in Italy(in Salvaterra di Casalgrande, Reggio Emilia), in China (Suzhou) and in the United States (Ohio, Franklin and Maine, Lewiston). In addition to these production sites, Modula can count several branches in Europe, America, Asia and Africa and a vast network of authorized distributors all over the world.
)